7. April 2022Peter Pionke
Bergische Uni: Neue Werkstoffe für den 3D-Druck
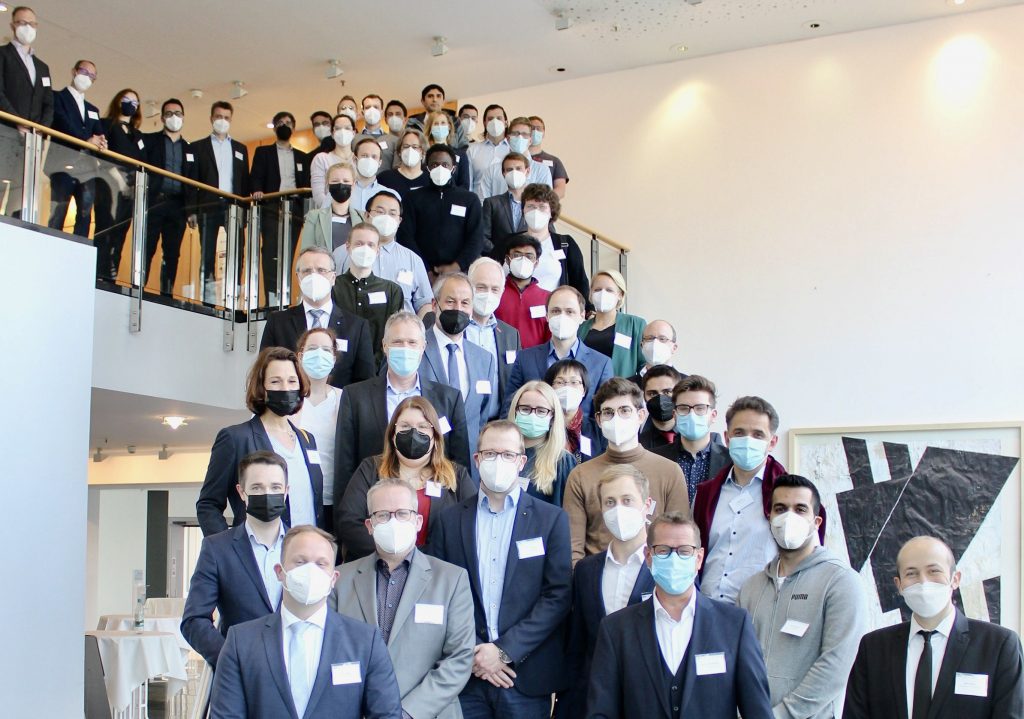
Mit vereintem Wissen und modernster Technik sowie finanzieller Unterstützung von insgesamt ca. sieben Millionen Euro für drei weitere Jahre durch die Deutsche Forschungsgemeinschaft (DFG) geht das Schwerpunktprogramm „Neue Materialien für die laserbasierte additive Fertigung“ (SPP2122) in die zweite Phase. Initiiert wurde diese vom stellvertretenden Programmsprecher Prof. Dr. habil. Bilal Gökce von der Bergischen Universität gemeinsam mit Prof. habil. Dr.-Ing. Stephan Barcikowski von der Universität Duisburg-Essen.
Bergische Uni seit Anfang 2022 Mitglied des Programms
Ende März führten beide Professoren durch die Auftaktveranstaltung mit insgesamt rund 60 Teilnehmenden sowie über 20 Fachbeiträgen. Der Lehrstuhl Werkstoffe für die Additive Fertigung um Prof. Gökce ist seit Anfang des Jahres Mitglied im Schwerpunktprogramm und vertritt mit dem Teilprojekt „Nanopartikel-Additivierung von Pulvern für die laserbasierte additive Fertigung von ODS Stählen“ die Materialforschung an der Bergischen Universität. Das Wuppertaler Teilprojekt wird mit ca. 400.000 Euro gefördert.
Ziel ist die Entwicklung eines neuen Stahlpulvers auf Eisen-Chrom-Basis für die additive Fertigung, sprich 3D-Druck. Solche Stähle werden beispielsweise in Kesseln und Turbinen von Kraftwerken eingesetzt, die Kohle oder Gas mit erneuerbaren Brennstoffen wie Biomasse verfeuern.
Die Erhöhung der Betriebstemperaturen von Kraftwerksturbinengeneratoren ist eine übliche Methode zur Verbesserung des Wirkungsgrads von Dampf- und Gasturbinen. „Der Betrieb einer Anlage bei höheren Temperaturen stellt jedoch extreme Anforderungen an die verwendeten Werkstoffe. Durch winzige keramische Nanopartikel im Material kann die Beständigkeit (Festigkeit, Kriechbeständigkeit) der Bauteile bei hohen Temperaturen verbessert werden“, erklärt Bilal Gökce. Diese gleichmäßig in das Material hinein zu bekommen, sei jedoch nicht einfach.
Verhalten der Nanopartikel verstehen
Der übliche Weg ist teuer und aufwändig, daher untersuchen Prof. Gökce und sein Team Verfahren der additiven Fertigung. Dabei werden unterschiedliche additive Fertigungsverfahren und Simulationen eingesetzt, um das Verhalten der Nanopartikel während der Verarbeitung zu verstehen und die richtigen Parameter zu finden, um möglichst feste Bauteile herzustellen. „Für Herstellung des für den 3D-Druck verwendeten Pulverkomposits, ebenfalls ein besonderes Thema im Projekt, kommen innovative Laserverfahren zum Einsatz“, so Gökce.
Das gemeinsam mit der TU Darmstadt (Prof. Dr. Bai-Xiang Xu) und dem Max-Planck-Institut für Eisenforschung (Dr. Baptiste Gault) angelegte Forschungsprojekt adressiert die additive Fertigung von oxiddispergierten Stählen (ODS) und hat die Entwicklung eines neuen Pulvers auf Eisen-Chrom-Basis für die additive Fertigung zum Ziel.
Link zum Wuppertaler Lehrstuhl: www.mam.uni-wuppertal.de
Link zum Schwerpunktprogramm: www.uni-due.de/matframe
Weiter mit:
Kommentare
Neuen Kommentar verfassen